The use of a wide scale, silicon carbide production capacity is still waiting to soar
Release time:
2023-10-30
With the accelerated evolution of the "new four modernizations" of automobiles, automotive chips have become one of the main growth points of the entire semiconductor market, and silicon carbide with excellent performance is a shining new star. Major chip companies around silicon carbide have begun large-scale expansion and acquisition. Major automakers are also worried about a renewed chip shortage and are scrambling to place orders and sign long-term supply agreements with chip makers. The wild road of silicon carbide has begun.
Electric vehicles will promote large-scale commercial use of silicon carbide
With the development of the new energy vehicle market, the market share of new energy vehicles in China has exceeded 28%. Some institutions predict that in 2030, global new energy vehicle sales will account for nearly 50% of new car sales in the year.
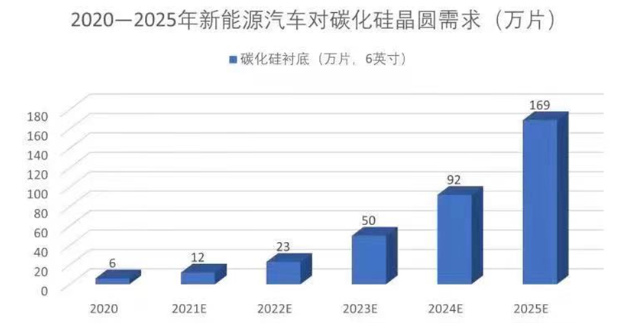
At present, silicon carbide power devices have been applied to key power systems inside new energy vehicles, including traction inverters, DC/DC converters, and on-board chargers. In the view of Victor Veliadis, chairman of the IEEE International Wide Bandgap Semiconductor Technology Roadmap Committee, electric vehicles and hybrid vehicles will become the "killer" application that will promote the large-scale commercial use of silicon carbide.
"Silicon carbide has a wider band gap than silicon, allowing for higher voltage blocking and is suitable for high power and high voltage applications. This can make DC/DC converters and on-board chargers more efficient, allowing electric vehicles to charge faster and last longer while reducing costs. That makes it extremely competitive." Victor Veliadis explains.
"There is less space inside the car, so increasing power density is the future trend." Compared to silicon, silicon carbide devices can not only make the packaging scheme of power semiconductors more compact, but also make the passive devices and heat sinks that are compatible with the power devices smaller." Qiu Qi, vice general manager of marketing of Taike Tianrun Semiconductor Technology (Beijing) Co., LTD., told China Electronics News.
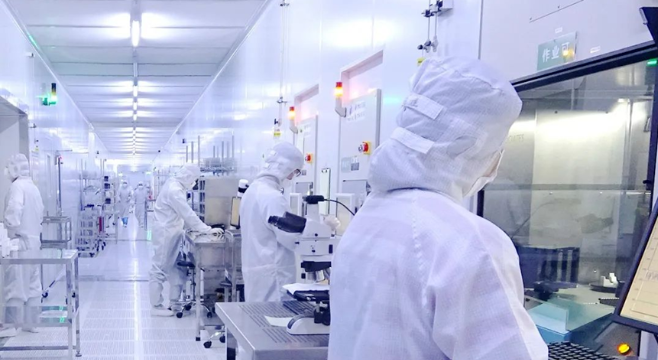
The excellent performance in reducing the size and improving the efficiency helps silicon carbide to successfully "get on the car". Specifically, the application of silicon carbide technology in new energy vehicles is mainly concentrated in two aspects. First, in the field of on-board chargers (OBC) and DC-DC power supplies, the power density of the system based on traditional silicon technology is less than 2KW/L, while the OBC system using silicon carbide technology can obtain a power density greater than 3KW/L, and its efficiency can also be increased from 95% in the past to more than 97%, saving energy for consumers. The second is in the field of main drive inverters. Lu Tao, head of China for automotive main drive inverter semiconductor of ON Mei Power Solution Department, told reporters: "The most direct performance of silicon carbide in the application of main drive inverter is to improve the efficiency of the system, and then make the same battery capacity, improve the car mileage." According to some feedback on the market, the main drive inverter with silicon carbide has been applied, and the efficiency has been improved by at least 2% or so, if the whole vehicle system is considered, it may be improved more. Now most of the new energy vehicle manufacturers are launching or preparing to launch the main drive inverter equipped with silicon carbide."
Due to the demand for fast charge, 800V high voltage systems are gradually entering the market vision. Lu Tao predicted that there will be more new energy vehicles using 800V systems in the next one to two years. The excellent performance of silicon carbide's low impedance and other characteristics under high pressure will also increase its market share.
Enterprises take multiple measures to enhance the stability of the industrial chain
With the increasing demand for silicon carbide devices in the automotive market, bringing market opportunities at the same time, but also accompanied by a bit of instability, whether it is chip manufacturers or automakers are aware of this, began to strengthen their silicon carbide supply chain, so as not to repeat the previous car chip shortage.
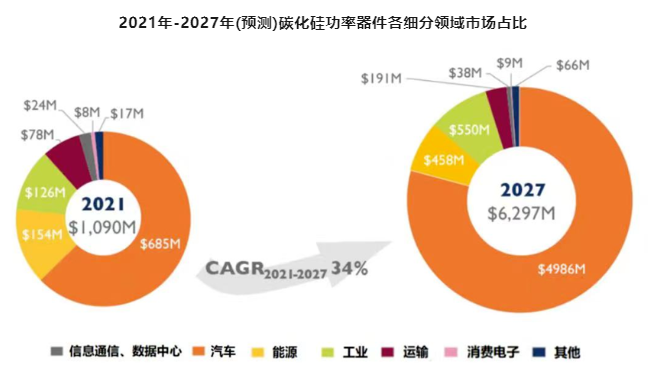
Wolfspeed, for example, announced that it would sell all of its RF business to MACOM, and the money from the deal would be used to expand its silicon carbide business. Renesas Electronics announces a 10-year silicon carbide wafer supply agreement with Wolfspeed; St announced a joint venture with SAN 'an OptoElectronics to mass-produce 200mm silicon carbide devices in China, as well as continued investments in Italy and Singapore to achieve annual silicon carbide revenues of more than $5 billion by 2030. Rohm reached an agreement with Solar Frontier to acquire the company's former Guofu plant, which will become Rohm's main production site for silicon carbide power semiconductors, and is expected to increase its silicon carbide capacity by 35 times in fiscal 2030.
At present, the high-end new energy vehicle devices are moving closer to or switching to silicon carbide, this phenomenon is particularly obvious in the 800V system, which is one of the reasons for the rapid development of the entire silicon carbide market. "However, the excessive development of any market will lead to a corresponding shortage of supply or overcapacity, which is reflected in the shortage of silicon carbide products in the past two years in new energy vehicles." Lu Tao told reporters.
Silicon carbide industry as a technology-intensive industry, the establishment of its wafer production line not only requires a lot of money and time, but also faces the difficult situation of purchasing key production equipment, complex silicon carbide device manufacturing process, and scarce related professionals, and its entry threshold is inextricably raised. Secondly, due to the high performance and reliability requirements for car-to-gauge silicon carbide power devices, only a few companies can provide them. These problems will lead to the current supply shortage of silicon carbide devices.
The challenge behind capacity is across the supply chain.
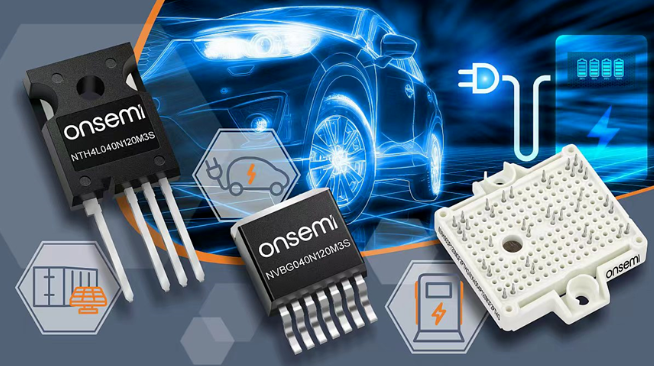
On is active in improving the silicon carbide supply chain, in order to obtain high-quality substrate production capacity and research and development capabilities, in the past two years acquired GT Advanced Technologies (GTAT). At the same time, ON also actively invested in the expansion of the extension plant of its Czech plant to ensure the production capacity of the extension; FAB expansion in Korea to enhance FAB capabilities.
Domestic silicon carbide enterprise Tyke Tianrun also adhere to IDM. Relying on its own wafer production line, it continues to accumulate experience in silicon carbide device manufacturing and production process, and further master the core technology. It began laying out an 8-inch silicon carbide production line in late 2022 and expects to reach 100,000 pieces per year in 2025. In terms of downstream enterprises, Taike Tianrun also actively cooperates with BYD, Wuling mini, GAC, Maserati, Geely, BAIC, Dongfeng and other car companies to further understand market demands.
"Recently, in order to ensure the security of the silicon carbide supply chain, the major silicon carbide enterprises are actively laying out and strengthening the connection with upstream and downstream enterprises." Yang Jungang told the "China Electronics News" reporter, "Moreover, new energy vehicles and silicon carbide devices are emerging markets, if the two joint research related technologies, is expected to develop more suitable for the market of new products."
Silicon carbide large-scale car still need to reduce cost and increase efficiency
Although the speed of silicon carbide car is very fast, but want to achieve large-scale and truly complete replacement of silicon car, cost reduction is still a key factor. The cost of silicon carbide is much higher than that of silicon power devices.
Qiu Qi told reporters that there are three main directions to reduce the cost of silicon carbide chips: first, improve the wafer size, under the premise that the cost of the flow sheet is not much different, the larger the wafer, the more available chips can be produced by a single wafer, the lower the cost of a single chip; The second is to reduce the chip area by cutting technology or groove design; The third is to improve the yield through process optimization.
At first, most silicon carbide manufacturers could produce 4-inch wafers, but with the development of substrate and epitaxial technology, large-size wafers became possible. At present, many silicon carbide manufacturers say their production line will expand from 6 inches to 8 inches. The most direct relationship between size and power devices is expressed in DPW (number of chips on a single wafer). On the United States field application engineer, China automotive main drive silicon carbide technical support expert Niu Jiahao made an example for reporters: "To 32mm² silicon carbide devices, for example, 6-inch wafers can produce about 450 devices, 8-inch wafers can produce about 850 devices, and the proportion of wafer edge chips will be greatly reduced."
However, simply increasing the size of the wafer does not improve efficiency. If the technology is not mature, then the advantage of "large wafers" may become a disadvantage. "We are not only concerned about DPW, more to look at GDPW (number of effective chips), GDPW/DPW is the real yield rate." "If you want to make chips in 8-inch wafers, you need a high-quality substrate, high-quality epitaxy and high-quality device fabrication. All three are necessary." Lu Tao said.
Niu Jiahao told reporters: "At present, there is no mass production of 8-inch silicon carbide wafer products on the market. There are many technical limitations to upgrading the silicon carbide wafer size from 6 inches to 8 inches. Since the substrate accounts for a significant proportion of the cost of a silicon carbide device, mainstream manufacturers are constantly striving to achieve more devices on a single substrate by increasing size and improving quality, and ultimately reducing costs."